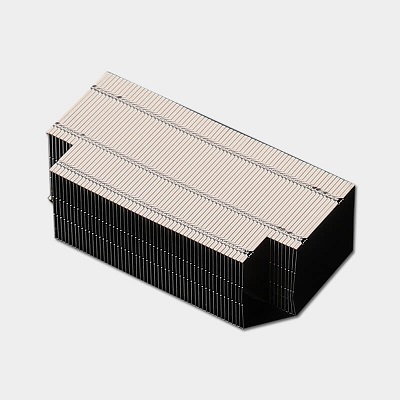
In the ever-evolving world of electronics, efficient heat dissipation is critical to ensure the longevity and optimal performance of devices. The increasing power and miniaturization of electronic components leads to greater heat generation, making thermal management a crucial consideration. Stamped heat sinks are a cost-effective and versatile option for thermal management in a wide range of applications. This guide will provide you with comprehensive information about stamped heat sinks, including their advantages, disadvantages, manufacturing process, and applications. We will also discuss the key factors to consider when selecting a stamped heat sink manufacturer, as well as the different materials that can be used for stamped heat sinks. By the end of this guide, you will have a thorough understanding of stamped heat sinks and be able to make an informed decision about the best solution for your specific needs, ensuring optimized device performance.
What is Stamping Heat Sink?
A stamped heat sink or stamped fin heat sink is a metal component that is manufactured by stamping a sheet of metal, typically aluminum or copper, into a finned design. The fins increase the surface area of the heat sink, which allows for more efficient heat transfer away from the heat source.
Stamped Heat Sink Manufacturing Process
Selecting the right material is the first step in the stamped heat sink manufacturing process. Aluminum and copper are the most common materials used for stamped heat sinks, as they offer good thermal conductivity and are relatively easy to work with.In the following sections, we will discuss the advantages and disadvantages of aluminum and copper heat sinks in more detail. We will also discuss other materials that can be used for stamped heat sinks, as well as the factors to consider when choosing a material for a specific application.
- Sheet metal stamping : The next step is to stamp the sheet metal into the desired shape. This is done using a stamping press, which applies a high force to the metal, causing it to deform into the desired shape.
- Finning : Once the heat sink has been stamped into the desired shape, the fins are created. This can be done using a variety of methods, including milling, broaching, and laser cutting.
- Finishing : The final step is to finish the heat sink. This may involve applying a coating to protect the surface from corrosion or oxidation, or it may simply involve cleaning the heat sink to remove any debris.
Heat Sink Manufacturers
Choosing the right heat sink manufacturer is important to ensure you get a high-quality product that meets your specific needs. When selecting a manufacturer, it is important to consider the following factors :
- Experience : The manufacturer should have experience in manufacturing heat sinks for the intended application.
- Expertise : The manufacturer should have a team of engineers with expertise in thermal management.
- Capabilities : The manufacturer should have the in-house capabilities to manufacture heat sinks to the required specifications.
- Quality : The manufacturer should have a commitment to quality and a robust quality control process in place.
- Customer service : The manufacturer should provide excellent customer service and be responsive to the needs of its customers.
Stamped Heat Sinks Performance
Stamped heat sinks offer several advantages over other types of heat sinks. These advantages include :
- Cost-effectiveness: Stamped heat sinks are relatively inexpensive to manufacture.
- Design flexibility : Stamped heat sinks can be customized to meet the specific needs of an application.
- Efficient heat transfer : Stamped heat sinks provide efficient heat transfer due to their increased surface area.
Custom Stamped Fin Heat Sinks vs. Other Solutions
While stamped fin heat sinks are an excellent choice in many scenarios, understanding alternatives is important. Machining heat sink fins might be needed for extremely intricate designs, while die casting heat sinks facilitate more complex geometries. When customization, cost-efficiency, and volume production are key, choose stamped fin heat sinks.
Stamping Heat Sink Materials
The choice of material is crucial in the design and effectiveness of stamping heat sinks. Aluminum and copper are the primary materials used due to their excellent thermal conductivity.
1. Aluminum
Aluminum is a popular choice for stamping heat sinks because of its favorable combination of thermal conductivity, lightweight nature, and cost-effectiveness. It efficiently conducts heat away from electronic components, aiding in their cooling. Aluminum is also known for its corrosion resistance, which ensures long-term durability in various operating environments.
2. Copper
Copper, with its exceptional thermal conductivity, outperforms aluminum in terms of heat transfer capability. This makes copper heat sinks highly efficient at rapidly dissipating heat. However, copper is heavier and more expensive than aluminum, which can impact overall product weight and cost. Copper heat sinks are often preferred in applications where maximizing thermal performance is crucial, such as in high-performance computing or industrial settings.
3. Composite Materials
In some cases, composite materials or hybrid designs are used for stamping heat sinks to harness the advantages of multiple materials. For instance, combining aluminum and copper can achieve a balance between cost-effectiveness and superior thermal performance.
It's essential to consider the specific thermal requirements of the application when selecting the material for stamping heat sinks. Factors such as thermal conductivity, weight constraints, and cost considerations play a vital role in determining the optimal material for efficiently managing heat in electronic devices.
Applications of Stamping Heat Sinks
Stamping heat sinks find versatile applications across multiple industries, owing to their efficiency, cost-effectiveness, and adaptability. Some key sectors where stamping heat sinks are prominently employed include:
1. Electronics
Stamping heat sinks play a pivotal role in cooling electronic components such as CPUs, GPUs, power transistors, and voltage regulators in computers, laptops, gaming consoles, and servers. Their compact design and excellent thermal performance help maintain the integrity and longevity of electronic devices.
2. Telecommuniction
In the telecommunications industry, stamping heat sinks help manage heat generated by various components in networking equipment, routers, switches, and base stations. These heat sinks ensure reliable operation and prevent overheating issues in critical communication infrastructure.
3. LED Lighting
LED lighting systems generate heat that can degrade performance and reduce lifespan. Stamping heat sinks efficiently dissipate this heat, making them indispensable in LED bulbs, streetlights, and architectural lighting applications.
4. Automotive Electronics
Stamping heat sinks contribute to the thermal management of automotive electronic systems. They are used in engine control modules (ECMs), infotainment systems, and advanced driver-assistance systems (ADAS) to ensure consistent and reliable performance under varying temperature conditions.
5. Industrial Equipment
Industrial machinery often relies on stamping heat sinks to control heat in motor drives, power supplies, and automation equipment. Their ability to operate in harsh industrial environments makes them a reliable choice.
6. Consumer Electronics
Stamping heat sinks can be found in everyday consumer devices such as gaming consoles, home appliances, and audio amplifiers. Their lightweight design and efficiency make them suitable for a wide range of applications.
7. Renewbale Energy
Stamping heat sinks are essential in renewable energy systems like solar inverters and wind turbine control systems. They help manage the heat generated during energy conversion, ensuring optimal performance and longevity of these systems.
8. Medical Devices
Medical equipment, such as MRI machines, diagnostic devices, and laser systems, benefits from stamping heat sinks to maintain stable operating temperatures, crucial for patient safety and precision diagnostics.
Read More : Home Appliance Metal Stamping Parts
Work with Experienced Stamping Heat Sink Manufacturer Feng Yu
Stamped fin heat sinks provide a powerful balance of adaptability, performance, and affordability for diverse thermal management needs. Partnering with a manufacturer specializing in copper processing parts, precision aluminum parts, and advanced stamping processes guarantees that you'll achieve the perfect cooling solution, safeguarding your electronic devices.
Feng Yu is a metal stamping parts manufacturer based in China and ISO 9001 certified, is your top choice for premium stamped heat sinks. With nearly 50 years of experience in precision metal processing, we specialize in crafting high-quality, efficient, and reliable heat sink solutions. Our state-of-the-art equipment and certified team guarantee that every heat sink we manufacture meets rigorous quality standards. Trust Feng Yu for precision, quality, and innovation in stamped heat sinks.
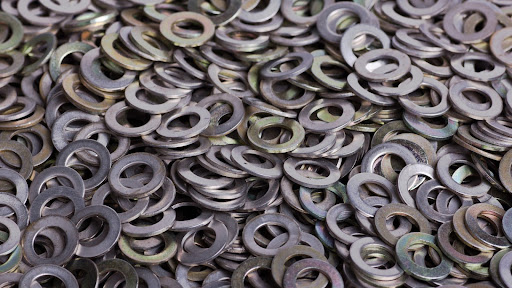
In the world of manufacturing and engineering, where precision reigns supreme, every component contributes to the final product's functionality, safety, and efficiency. Often overlooked yet essential, precision metal shims play a vital role.
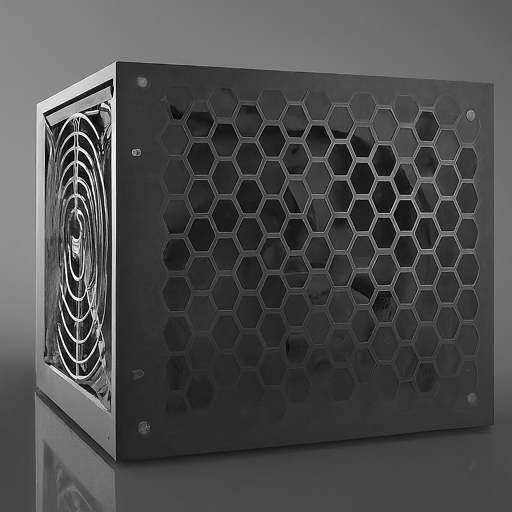
In the world of electronics, power supply units (PSUs) play a critical role in converting electrical energy, ensuring devices receive the correct voltage and current for optimal operation. To safeguard their components and manage heat, PSUs require durable and efficient enclosures. This is where metal stamped power supply shells excel.
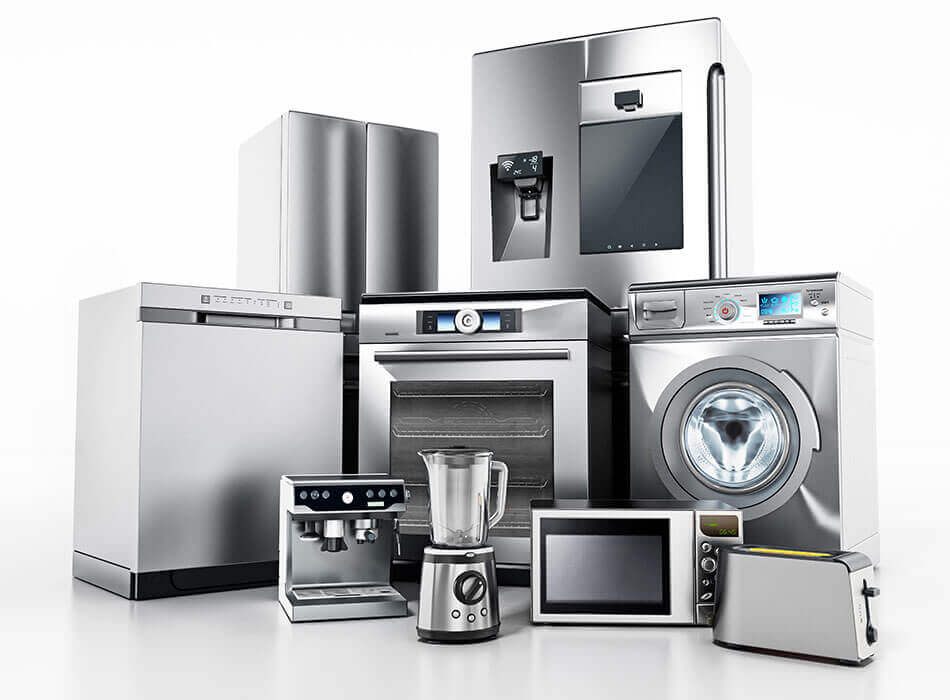
Custom-stamped appliance components are the backbone of products we rely on daily, from refrigerators to washing machines. To ensure appliances work efficiently and safely, these components must be manufactured to precise specifications. This involves challenges such as ensuring accurate dimensions and choosing materials with the right properties for each part.