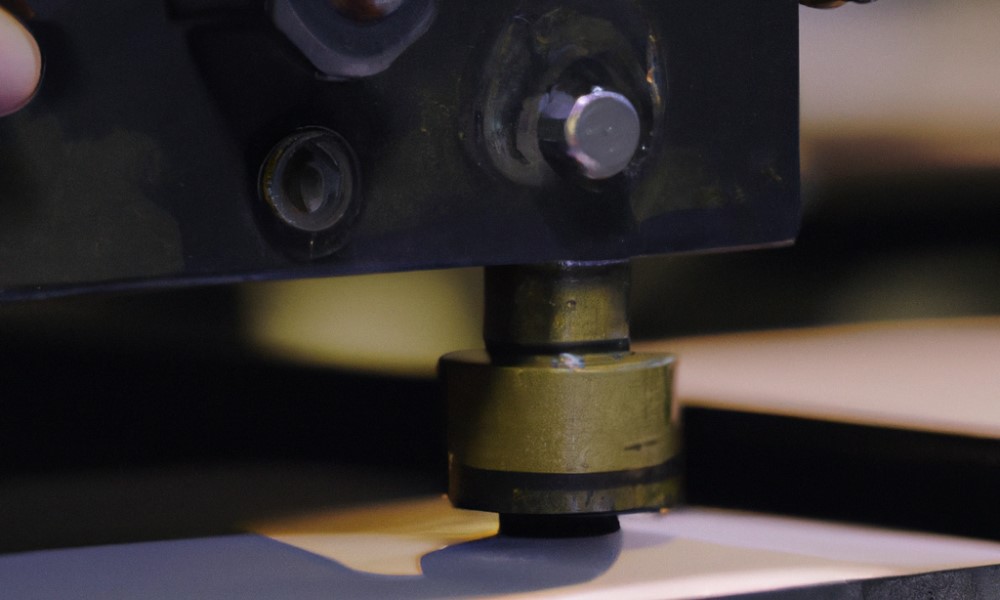
Metal Stamping parts are pieces of metal that are shaped by applying an intense force through a die. Metal blanks are inserted into dies and then pressed to create specific shapes. Commonly stamped items include car body panels, engine components, and household appliances.
Frequently used stamping materials
Stamping is a manufacturing process that can be used with many different materials, including metals such as steel, aluminum, brass, and copper; composite plastics; or other special types of materials. It depends largely on what you want the finished product to look like: whether it's hardy yet malleable enough or whether it has all the qualities you need when pressing it into certain shapes. In most cases though - metal remains the primary material because it withstands pressure while remaining malleable enough to form various shapes without breaking.
What equipment is needed for metal stamping?
The equipment needed for metal stamping depends on the specific requirements of the stamping process, as well as the type and size of the parts being produced. In general, the main pieces of equipment needed for metal stamping include:
- Stamping press: This is the main piece of equipment used in the stamping process. A stamping press applies force to the stamping die, which cuts and forms the metal into the desired shape. Stamping presses are available in a range of sizes and configurations, depending on the specific requirements of the stamping process.
- Stamping die: This is a specialized tool that is used to cut and form the metal parts. The die is typically made of hardened steel and is precision-machined to match the desired shape of the finished part.
- Workpiece: This is the piece of metal that will be formed into the desired shape. The workpiece is placed on the press bed and positioned so that it lines up with the stamping die.
- Press bed: This is the stable base on which the stamping press, stamping die, and workpiece are positioned during the stamping process.
- Bolster plate: This is a plate that provides support for the stamping die and workpiece during the stamping process.
- Hydraulic or mechanical system: This is the system that powers the stamping press, providing the force needed to cut and form the metal parts.
- Other pieces of equipment that may be needed for metal stamping include automatic feed systems, safety guards, and handling equipment to move the finished parts.
The most critical equipment is stamping die
The main tool used for stamping is a stamping die. A stamping die is a specialized tool that is used to cut and form metal parts into specific shapes. The die is typically made of hardened steel and is precision-machined to match the desired shape of the finished part. The die is placed into a stamping press, along with a piece of metal (called a blank) that will be formed into the desired shape. The press applies force to the die, which forces metal material into its ideal form while simultaneously leaving behind small bits in order to ensure that every single cut and forming process is perfect.
The general overview of the stamping process
The specific steps and details of the stamping process may vary according to the specific requirements of the stamping process and the equipment used, while the basic steps of the stamping process are as follows:
- Design and create the stamping die: The first step in the stamping process is to design and create the stamping die that will be used to cut and form the metal parts. The die is typically made of hardened steel and is precision-machined to match the desired shape of the finished part.
- Set up the stamping press: The next step is to set up the stamping press, which will be used to apply force to the stamping die and form the metal parts. This involves placing the stamping die into the press and securing it in place, as well as positioning the workpiece (the piece of metal that will be stamped) on the press bed.
- Load the workpiece: The workpiece is placed onto the press bed, either manually or using an automatic feed system. The workpiece is positioned so that it lines up with the stamping die.
- Close the press: The press is then closed, which brings the stamping die into contact with the workpiece.
- Apply force: The press applies force to the stamping die, which cuts and forms the workpiece into the desired shape. The amount of force applied will depend on the specific requirements of the stamping process and the properties of the material being used.
- Remove the finished part: Once the stamping process is complete, the finished part is removed from the press. The stamping die is then opened, and the scrap material (the excess metal that was not formed into the desired shape) is removed.
-
Repeat the process: The stamping process is then repeated to produce additional parts, as needed.
Common applications of metal stamping
Some common applications for metal stamping include:
- Automotive industry: Metal stamping is widely used in the automotive industry to produce a wide range of parts, including car body panels, engine components, and other parts.
- Appliances industry: Metal stamping is commonly used to produce parts for household appliances, such as washing machine drums, refrigerator door panels, and stovetop burners.
- Electronics industry: Metal stamping is used to produce parts for a variety of electronic devices, such as computer cases, cell phone housings, and other components.
-
Medical industry: Metal stamping is also used in the medical industry to produce parts for a wide range of medical devices and equipment, such as surgical instruments and implantable devices.
Feng-Yu Precision Electronics Co., Ltd. is a China custom metal stamping manufacturer that was founded in 1971, based on our mastery of precision hardware processing technology and nearly 50 years of experience. Hardware processing provides key components for many industrial equipment and products, such as processing hardware stamping parts, injection molding parts, automotive stamping parts, precision hardware stamping parts, medical devices stamping, and other products. Our company provides a one-stop service process from drawing receiving to sample delivery, with stable quality and commitment, please contact us.
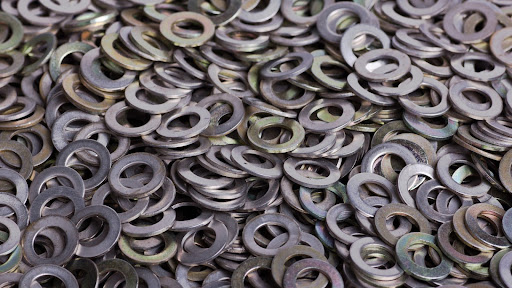
In the world of manufacturing and engineering, where precision reigns supreme, every component contributes to the final product's functionality, safety, and efficiency. Often overlooked yet essential, precision metal shims play a vital role.
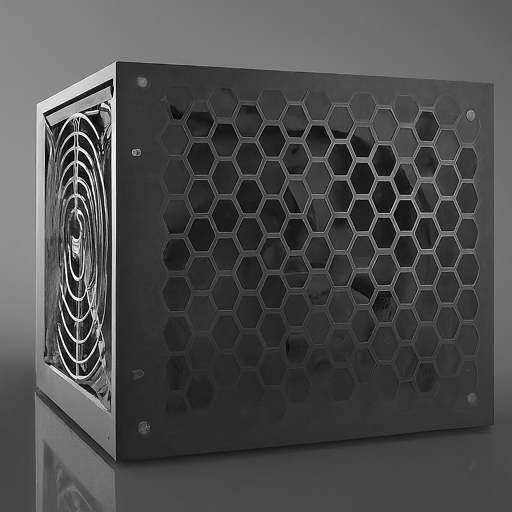
In the world of electronics, power supply units (PSUs) play a critical role in converting electrical energy, ensuring devices receive the correct voltage and current for optimal operation. To safeguard their components and manage heat, PSUs require durable and efficient enclosures. This is where metal stamped power supply shells excel.
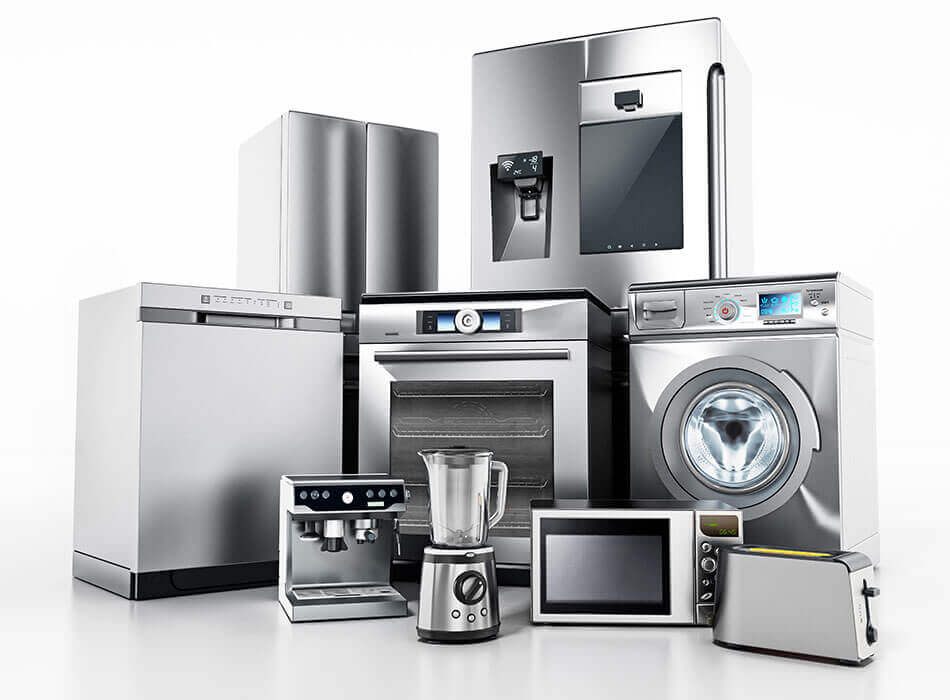
Custom-stamped appliance components are the backbone of products we rely on daily, from refrigerators to washing machines. To ensure appliances work efficiently and safely, these components must be manufactured to precise specifications. This involves challenges such as ensuring accurate dimensions and choosing materials with the right properties for each part.