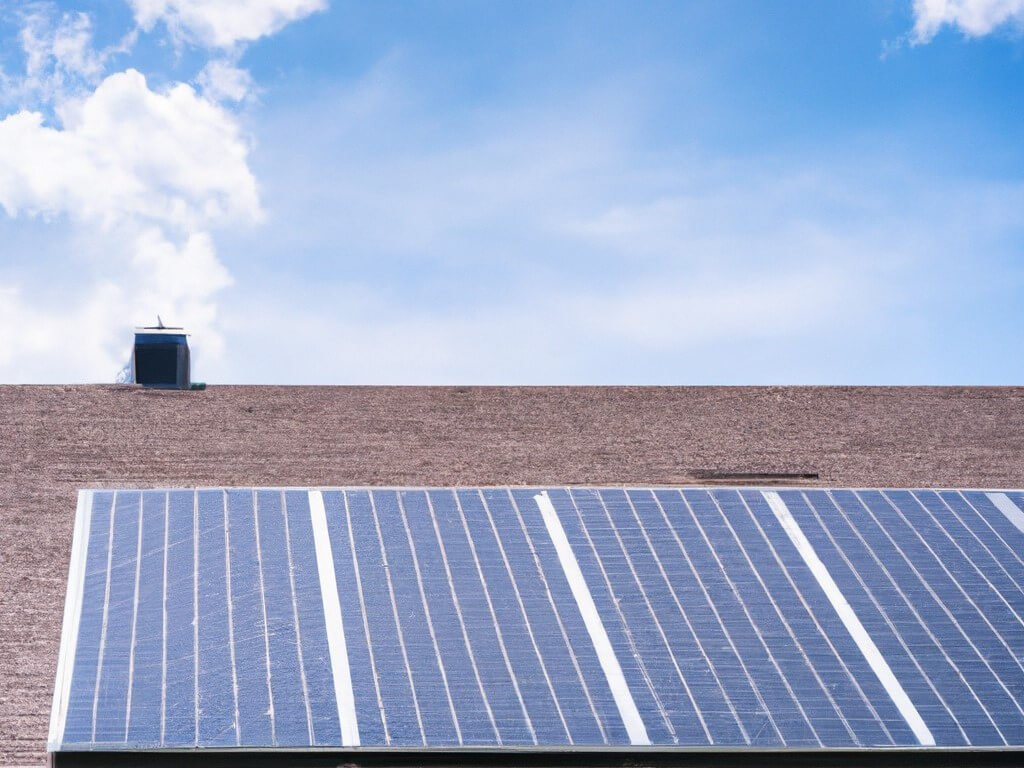
Introduction:
Solar panel fixing brackets are made using metal stamping technology which is a cost-effective method of producing high-quality metal parts with precision and accuracy, that ensures their durability, strength, and accuracy.
In this article, we will explore the art of metal stamping and how solar panel fixing brackets are made using this process. We will discuss the various stages involved in metal stamping and how it contributes to the creation of high-quality solar panel fixing brackets.
The Process of Metal Stamping
The process of metal stamping involves a series of steps, starting with designing the product and preparing the metal sheet. The metal sheet is then fed into the stamping press, where a series of dies cut and shape the metal into the desired shape. The metal is then bent, folded, or punched to create additional features or details.
How Solar Panel Fixing Brackets are Made Using Metal Stamping
Solar panel fixing brackets are an important component of solar panel installations. These brackets are used to hold the solar panels in place and ensure that they are securely attached to the roof. Metal stamping is used to create these brackets, as it allows for precise shaping and cutting of the metal sheets.


To create solar panel fixing brackets using metal stamping, the design is first created using computer-aided design (CAD) software. The metal sheet is then prepared and fed into the stamping press. The dies are set up to cut and shape the metal into the desired shape, which is then bent and punched to create the necessary features. The brackets are then inspected for quality control before they are packaged and shipped to the customer.
Material Selection
Choosing the right materials for solar equipment brackets is crucial for ensuring their longevity, performance, and overall system reliability. The utilization of SGCC galvanized steel plates provides numerous benefits, including durability, corrosion protection, cost-effectiveness, sustainability, and ease of installation. By opting for SGCC galvanized steel, solar equipment manufacturers and installers can enhance the structural integrity of their installations, leading to increased efficiency and long-term savings.
Advantages of Using SGCC Galvanized Steel Plate for Brackets
-
Durability and Weather Resistance
SGCC galvanized steel plates are renowned for their exceptional durability and weather resistance properties. The hot-dip galvanization process creates a protective barrier that shields the steel surface from moisture, corrosion, and harsh weather conditions. This ensures the longevity and structural integrity of the solar equipment brackets, even in challenging environments.
-
Corrosion Protection
One of the primary benefits of SGCC galvanized steel plates is their superior corrosion resistance. The zinc coating acts as a sacrificial layer, preventing the underlying steel from coming into direct contact with corrosive agents. As a result, the brackets remain protected against rust, oxidation, and other forms of corrosion, even when exposed to moisture or extreme weather conditions.
-
Cost-Effectiveness and Efficiency
SGCC galvanized steel plates offer a cost-effective solution for solar equipment brackets. Their durability and corrosion resistance minimize the need for frequent repairs or replacements, resulting in long-term cost savings. Additionally, the galvanization process is highly efficient, providing uniform coverage and optimal protection to the steel surface, ensuring reliable performance throughout the equipment's lifespan.
3 Steps for Metal Stamping Solar Fixed Backsheet
- To create a solar panel fixing bracket, the first step is to design the metal stamping die of the fixing bracket on a computer. This design is then sent to a machine called a stamping press.
- After the metal stamping dies of the fixing bracket are designed, the second step is die assembly, testing, and proofing: The stamping press uses a die and punches set to cut and shape the metal sheet into the desired shape. The die and punch set is made up of two components: the die, which is a specially designed block that contains the negative image of the desired shape, and the punch, which is the component that physically stamps the metal into the shape of the die.
- The third step is put into mass production: As the stamping press operates, the metal sheet is fed into the press and is cut and shaped by the die and punch set. This process can be repeated multiple times to create several identical parts. Once the stamping is complete, the parts are then cleaned, deburred, and inspected for quality control.
Video of Solar Panel Fixing Bracket Metal Stamping Process
Quality Control in Metal Stamping
Quality control is an important aspect of the metal stamping process. The brackets must be inspected for dimensional accuracy, surface finish, and material properties to ensure that they meet the required specifications. Various inspection methods are used, such as visual inspection, coordinate measuring machines (CMM), etc.


Conclusion
The art of metal stamping is a crucial process in the manufacturing industry, and it plays an important role in the production of solar panel fixing brackets. The process requires precision and expertise, and it involves a series of steps that require attention to detail. By using advanced technology and quality control methods, manufacturers can create high-quality products that meet the required specifications.
Feng-yu is a professional electronics metal stamping services provider, if you have any needs for electronics metal stamping, such as solar panel fixing brackets, contact us!
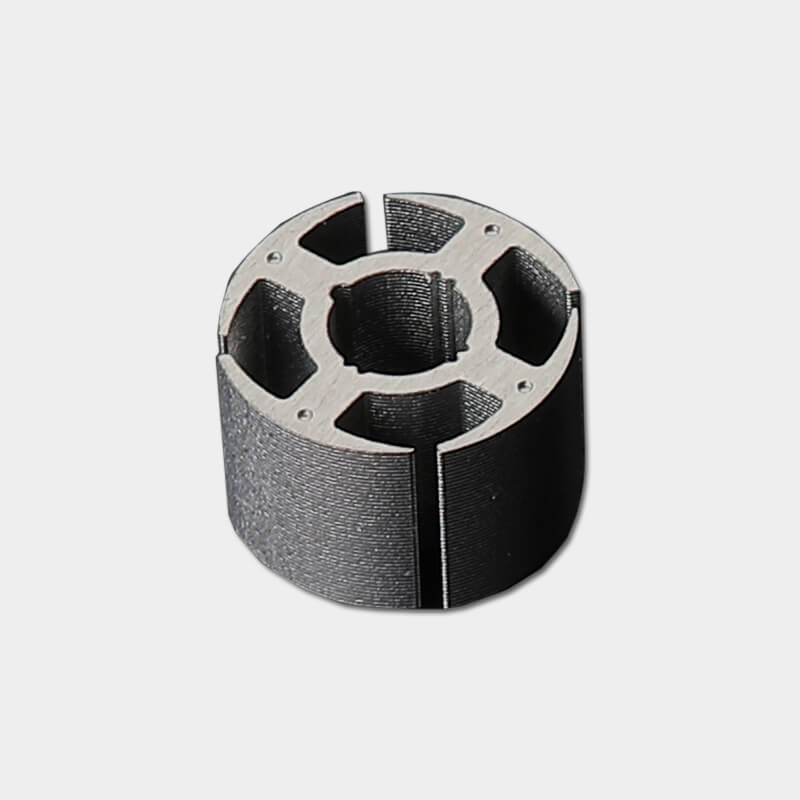
Metal stamping is essential for motor core manufacturing , providing precise shaping, high-volume production, and quality control measures.
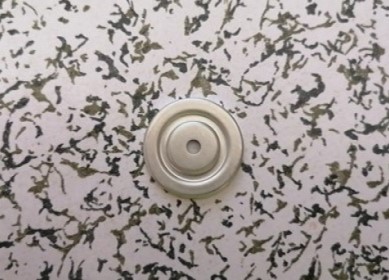
Metal stamping is essential for manufacturing pressure stabilizing gaskets, providing precise shaping, high-volume production, and quality control measures.
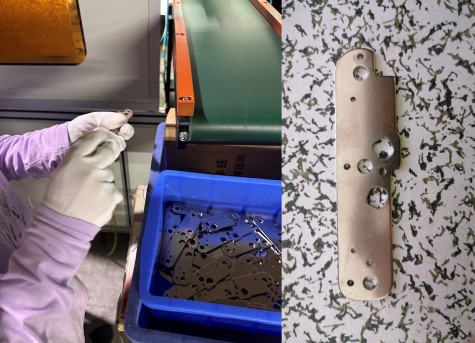
Metal stamping is crucial for producing stable, precisely positioned brackets in car audio systems. It offers cost-effective, high-quality manufacturing and adapts to advancements, including new materials, automation, and sustainability. Contact us for your precision metal stamping needs.