Welcome to the continuation of our exploration into the challenges of metal stamping miniature components. In "Part 2," we unravel the final two hurdles, providing a comprehensive overview of this demanding industry. Alongside these challenges, we delve into real-world case studies, showcasing innovative solutions and meticulous craftsmanship. Join us as we conclude our exploration, gaining a deeper understanding of the intricate processes and technologies that define the world of metal stamping miniature components
9. Cost Considerations
Stamping small parts often incurs higher per part costs compared to stamping larger parts. This is primarily driven by the higher tooling costs required for stamping small parts. The stamping dies and supporting tooling involved in metal stamping have high fixed costs regardless of part size. But with small parts, the production volumes are usually lower, so the fixed tooling costs get spread across fewer parts.
In addition, because small parts are more intricate and complex, the tooling itself tends to be more sophisticated and expensive. This further increases the fixed costs that have to be accounted for. The more detailed the part geometry, the more complex the die components need to be.
Moreover, small parts often require secondary processing after stamping, such as deburring, cleaning, heat treatment, plating, etc. And the cost of these secondary operations on a per part basis is higher with lower volumes.
The combined effect is that small part stamping results in a higher per piece cost compared to high volume production of larger, less intricate parts. Therefore, cost reduction strategies need to be explored. This includes investigating alternative materials, engineering the parts for easier processing, tooling optimization, lean manufacturing techniques, and increasing volumes whenever possible. Getting the lowest possible cost per part requires addressing the cost drivers throughout the entire stamping process chain.
10. Quality Control
Controlling quality is always important in metal stamping, but can be especially challenging with small parts. The small size makes effective inspection more difficult, as tiny defects are harder to detect visually. At high production volumes, manual inspection becomes impractical. Small parts may require specialized inspection equipment like optical comparators, vision inspection systems, or automated sorting machines.
If using automated systems, the fixturing and handling of tiny parts presents difficulties. Parts can shift during inspection, producing false rejects. Cleanliness is also critical, as any debris or dust can obscure defects in small features. And with less material, small parts are more prone to accidental damage during handling between processes.
Stamping shops need robust quality control plans for small parts, with well-designed inspection points, gauging, and sample sizes. Issues like burrs, flash, warped or bent parts, and coating flaws become major defects on miniature components. And when problems arise, root cause analysis is essential to identify and correct the source rather than just scrapping parts. Proactive process monitoring and control techniques are key to minimizing defects and maintaining tight tolerances when stamping small metal parts.
Case Study
1. Stator / Silicon Steel Material Metal Precision Stamping Parts
Our venture into the realm of stator manufacturing brought forth the challenge of stamping precision parts from silicon steel material. The intricacies of working with silicon steel demanded a meticulous approach to maintain the structural integrity of the stator. Through a combination of advanced technology and skilled craftsmanship, we successfully produced high-quality stator components that adhere to stringent industry standards.
2. Stator embedding / Silicon Steel.PBT Material Metal Precision Stamping Parts
In the pursuit of excellence, we encountered the unique challenge of embedding stators with PBT material in addition to silicon steel. This dual-material requirement demanded a refined process design to seamlessly integrate both materials. Our precision stamping parts, born from the collaboration of silicon steel and PBT, stand as a testament to our commitment to innovation and adaptability in the face of diverse challenges.
3. Micro Motor Stator / Copper+PBT Material Metal Precision Stamping Parts
Micro motor stators posed a distinct challenge due to the use of copper and PBT materials. Achieving precision in stamping these intricate components required not only advanced technology but also a profound understanding of material characteristics. Our skilled team successfully navigated the complexities, delivering micro motor stators that meet the highest standards of quality and reliability.
4. Stator / Silicon Steel Sheet Material Precision Stamping Parts
Stamping stators from silicon steel sheet material presented its own set of challenges. The thin and delicate nature of the material required a careful balance between force and finesse during the stamping process. Our expertise in handling silicon steel sheets allowed us to produce flawless stator components, ensuring optimal performance in the final product.
5. Maglev / SUS430 Stainless Steel Material Metal Precision Stamping Parts
The challenge of stamping Maglev components from SUS430 stainless steel material pushed the boundaries of precision. Working with stainless steel demands a high level of accuracy to achieve the desired form and functionality. Through rigorous testing and refinement, we successfully delivered Maglev components that meet the exacting standards of durability and performance.
6. USB Port / SUS304 Material Metal Precision Stamping Parts
Stamping USB ports from SUS304 material brought to light the necessity for precision and durability in electronic components. The use of SUS304 stainless steel material demanded a keen focus on corrosion resistance and structural integrity. Our commitment to excellence ensured that the stamped USB ports not only met but exceeded industry expectations in terms of reliability and longevity.
Contact the Custom Plastic Molding Experts at Feng Yu Today
In conclusion, navigating the intricate landscape of metal stamping miniature components presents a series of formidable challenges that demand precision, expertise, and a commitment to innovation. As a leading manufacturer in the field, we understand the complexities involved and have consistently risen to the occasion, delivering high-quality miniature components that meet and exceed industry standards.
Our dedication to overcoming challenges is underlined by our investment in cutting-edge technology, meticulous process design, and a team of skilled craftsmen who bring a wealth of experience to the table. As we continue to evolve in this dynamic landscape, we invite you to explore our expanded production capabilities. Our commitment to staying at the forefront of technological advancements enables us to not only tackle current challenges effectively but also anticipate and address future industry trends.
Stay connected with our latest updates, company news, and valuable insights such as Metal Stamping for Automotive or Micro Motor Cooling Fan Stamping Metal Parts into the world of metal stamping miniature components. To discover more about our enhanced production capabilities and to stay informed about our company's progress, contact us today !
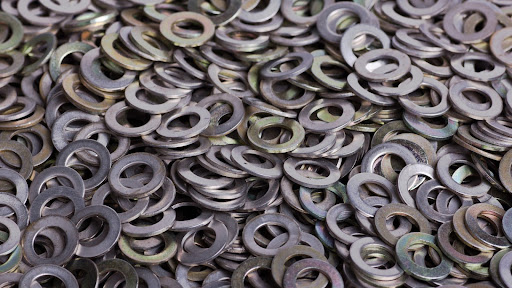
In the world of manufacturing and engineering, where precision reigns supreme, every component contributes to the final product's functionality, safety, and efficiency. Often overlooked yet essential, precision metal shims play a vital role.
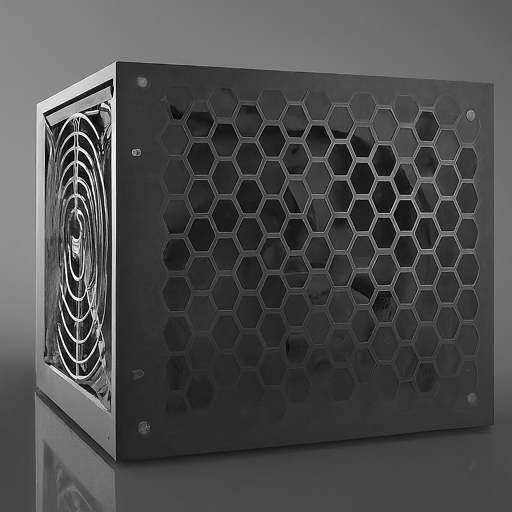
In the world of electronics, power supply units (PSUs) play a critical role in converting electrical energy, ensuring devices receive the correct voltage and current for optimal operation. To safeguard their components and manage heat, PSUs require durable and efficient enclosures. This is where metal stamped power supply shells excel.
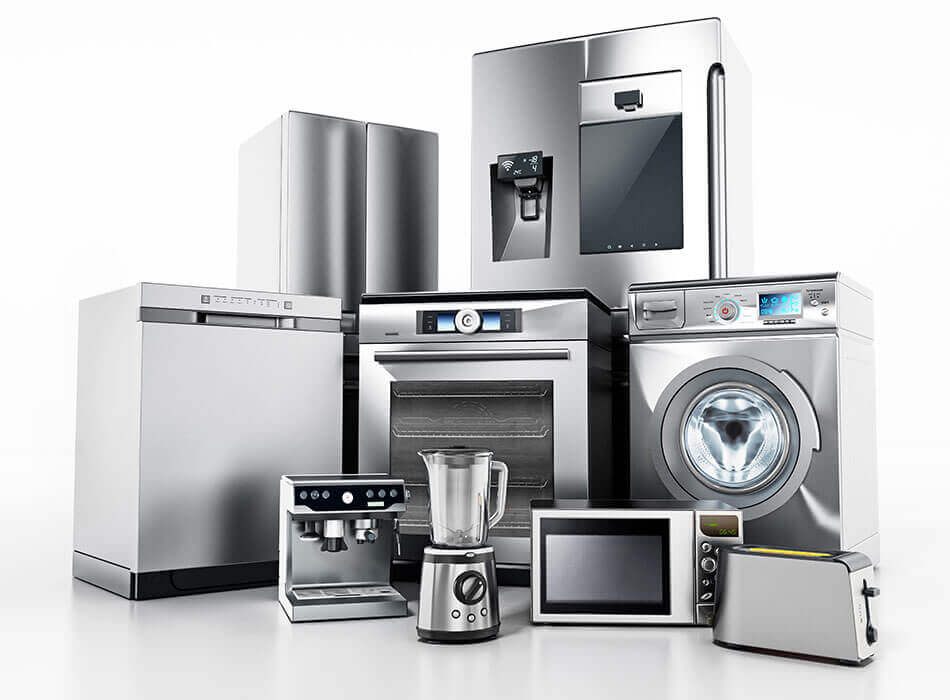
Custom-stamped appliance components are the backbone of products we rely on daily, from refrigerators to washing machines. To ensure appliances work efficiently and safely, these components must be manufactured to precise specifications. This involves challenges such as ensuring accurate dimensions and choosing materials with the right properties for each part.